Construction and application of a small PROFIBUSDP network
Introduce PROFIBUS-DP and the fieldbus network of pure master-slave communication constructed by its communication interface module. The network configuration is realized by the special networking tool SYCON; and the application of small boilers is implemented to realize the control of each controlled object. Monitoring.
Keywords: PROFIBUS-DP field bus; master node; network configuration
Shanghai 200072, China)
Keywords: PROFIBUSDP fieldbus; master node; network configura tion
(1) PROFIBUS-DP: used for communication between device-level control system and distributed I / O. It is designed for high-speed data transmission at the device level. (2) PROFIBUS-PA: Designed specifically for process automation, it allows sensors and actuators to be connected on one bus and has intrinsic safety specifications. (3) PROFIBUS-FMS: used for workshop-level monitoring network, is a token structure, real-time multi-master-slave network.
Among them, PROFIBUS-DP uses the layer 1 and layer 2 of the OSI reference model and the user interface. The user interface stipulates the application functions that can be called by the user and the system and different devices, and details the device behavior of various PROFIBUS-DP devices; the physical layer transmission uses the RS485 standard, this structure ensures the real-time communication and system Realized low cost. The protocol structure is shown in Figure 1.
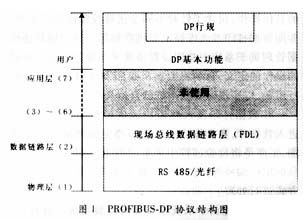
The PROFIBUS-DP data link layer provides the following transmission services:
(1) Send a message requesting confirmation (SRD service): send a message to a slave station, requesting the slave station to confirm. (2) Broadcast messages that do not require confirmation (SND service): send a message to a group of slave stations to start the corresponding SDN service without requiring confirmation from the slave stations.
The data transmission between DPM1 and DP slaves is divided into three stages: parameter setting, configuration, and data exchange. In the parameter setting stage, each slave station compares its actual configuration data with the configuration data received from DPM1. Only when the actual data matches the required configuration data, the DP slave station enters the user data transmission phase. Therefore, the device type, data format, length, and number of inputs and outputs must be consistent with the actual configuration. In the actual system, to enable the correct network communication between the master node and each slave station, the network must be configured, the relationship between the master station and the slave station must be specified, which slave stations are included in the information exchange cycle, and then Download the network configuration information to the PROFIBUS-DP master station.
PROFIBUS devices have different performance characteristics (different existing functions or different possible bus parameters). These parameters are different for each device type and each manufacturer. To enable PROFIBUS to achieve a simple plug-and-play configuration, these characteristics need to be specified in the device database (GSD). The GSD file is prepared by the manufacturer for each device type and provided to the user in the form of a device database list. This file format makes it easy to read out the device configuration information of any PROFIBUS? DP device, and automatically uses this information when configuring the bus system; the system automatically checks and verifies the data input errors and consistency before and after related to the entire system. ?
2.1 System hardware configuration This system is mainly composed of a master network node (a type of master station) and a field intelligent unit (DP slave station) to form a distributed network data monitoring system. The block diagram of the system structure is shown in Figure 2. After the networking is completed by the networking equipment, the master and slave send or request data through the master station, and the slave station responds or confirms the data sent by the master station to complete the data transmission of the PROFIBUS network.
2.1.1 Master station node In this system, the master station interface module uses the Swedish ANYBUS PROFIBUS-DP Master module [3]. The module is an embedded device. It has all the functions of a class of master station, supports the communication baud rate from 9.6kbit / s to 12M bit / s, and can connect up to 124 slave stations. Interface with user CPU through 2K dual-port RAM (DPRAM) on the hardware. The dual-port RAM area also includes system information area, hardware information area and handshake flag. Its I / O data sending area and data requesting area are both up to 512 bytes, and an expansion buffer can be opened. Provide mailbox messages on the software to exchange information with the user's CPU.
In this system, the node of the master station monitors the status of the entire system through the communication relationship established with the slave stations. The master node uses the ATMEL89C52 chip as the CPU, together with the PROFIBUS-DPMaster interface module to form the master node of the PROFIBUS network to realize the management of the network nodes. The CPU and static memory exchange data with the dual-port RAM of the interface module through the data line, address line and control line. The data content mainly includes the process data, status information and buffer configuration information of each slave node. An electrically erasable memory (EEPROM) with a watchdog function is used to store the operating parameters of the master node, the networking information of the fieldbus network, and the node status information. The static memory (RAM) serves as a data memory to store the process data of the slave nodes. The structure of the master node is shown in the upper part of Figure 2.
2.1.2 Field intelligent unit (DP slave)
In this system, the PROFIBUS-DP slave station interface module uses the Swedish ANYBUS-SPROFIBUS-DP module? [4]. Similar to the main module, it is also an embedded device. The hardware interfaces with the user's CPU through 2K dual-port RAM (DPRAM). The field intelligent unit uses 51 series single-chip microcomputer as the core processor, which mainly completes the initialization of the PROFIBUS slave module, including the allocation of the I / O mapping area-the allocation of the mapping area address, the length setting, and then the address allocation according to the interface mapping area Read and write I / O data. The PROFIBUS slave station interface module is embedded in the field intelligent unit, receives control commands, and provides various system parameters required by the master station. The structure of the field intelligent unit is shown in Figure 3.
The on-site intelligent unit collects and processes the working parameters and state parameters of the controlled object, and writes information and data to the input mapping area of ​​the DP slave module for the master node in the network to read and monitor the host computer; at the same time, it outputs from The mapping area reads the control information sent by the node of the master station, and after judgment, makes control decisions on the controlled object.
2.2 Communication network construction of the system?

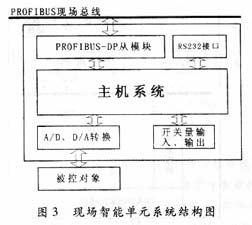
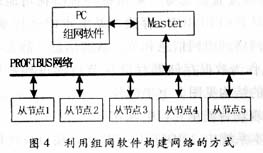
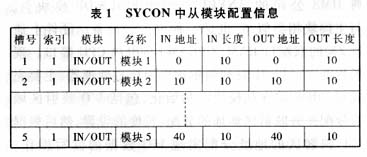
Rechargeable Handheld Vacuum cleaner: This Mini Vacuum Cleaner can be used for cleaning hidden dirty of notebook keyboard, printer, pet food, office, kitchen table, or other small household appliances.
Car mini vacuum cleaner: This Usb Vacuum cleaner can be used for cleaning car vent, dashboard, storage cabinet, sand, dust, paper, food debris, and so on.
Rechargeable wireless vacuum cleaner: this vacuum cleaner power supplied by usb port, which is very easy and convenient to use and store.
Easy to use: this mini vacuum cleaners` filter can be washed by water. Just open the dust pot and take it out, then wash it clean and use it again after it dry.
Cordless Vacuum Cleaner,Cordless Mini Vacuum,Cordless Car Vacuum,Rechargeable Handheld Vacuum
SHENZHEN HONK ELECTRONIC CO., LTD , https://www.honktech.com